Top 6 Heavy-Duty Truck Fleet Management Mistakes and How to Avoid Them

Heavy-duty trucks move approximately 72.2 percent of the nation’s freight (over 10 billion tons).
Heavy-duty truck fleets play a critical role in keeping the country running smoothly. For drivers to do their jobs correctly, though, they need guidance from leaders who understand proper fleet management.
In this guide, you’ll learn about six common truck fleet management mistakes, as well as how to avoid them.
Mistake #1: Using Confusing Strategies
As a fleet manager, you know how important it is to follow plans and implement processes for your drivers to follow.
Some managers make the mistake of developing plans and processes that are confusing and difficult to follow. They may also have unrealistic expectations that create extra frustration and set their employees up for failure.
Confusing strategies can lead to increased employee turnover. It also leads to inefficient use of time, hindering productivity and performance.
What to Do Instead
When developing a plan, start with specific, measurable goals. Clarify what you want to accomplish. Then, think about how you’ll monitor progress and identify what is or isn’t working.
Straightforward plans and processes help you set clear expectations for your employees. They also help you measure performance more accurately, make wiser business decisions, and adapt to change more quickly.
Mistake #2: Skipping Vehicle Maintenance
Regular vehicle maintenance is essential to heavy-duty truck fleet management. If you don’t prioritize maintenance, your drivers could end up facing breakdowns, which slows down delivery times and hinders your productivity and profitability.
Skipping maintenance can also lead to expensive repairs, added fuel costs, and decreased driver safety. None of these things are conducive to a successful business.
What to Do Instead
It’s easy to forget about vehicle maintenance when your trucks are always in different places. However, regular maintenance is too important to skip.
Create and stick to a maintenance schedule, and prioritize preventative measures (oil changes, filter changes, tire rotation, brake checks, etc.). It’s easier (and much more affordable) to prevent problems than to fix them, so it makes sense to focus on prevention.
Mistake #3: Not Using the Right Technology
If you’re worried about how you’re going to keep up with a maintenance schedule for your fleet, it might be because you’re not using the right technology — or any technology at all.
Some managers are intimidated by the new fleet management technology options, such as fleet management apps and software. Don’t let a lack of familiarity with these tools stop you from using them, though. They offer numerous benefits that make life easier for fleet managers and other professionals in your field.
What to Do Instead
Look for fleet management software that offers essential features, including these:
- GPS tracking
- Hours of Service (HOS) compliance
- Route performance
- Maintenance and diagnostics
- Safety features (such as dash cams)
- Fuel consumption
- Vehicle idling
Fleet management software gathers valuable data that can help you better understand your drivers and ensure they’re maximizing productivity. These tools also create reports that clearly present this data and make it easier to track progress and performance.
Mistake #4: Not Collecting or Misreading the Data
If you’re not using fleet management software, you’re likely not collecting data that could help you improve your management strategy.
However, even those who do use fleet management software and collect data consistently might not benefit from it if they don’t read it correctly. Misreading data can cause you to make decisions that harm the business and interfere with productivity.
What to Do Instead
Look for fleet management technology that can interpret large volumes and data. It should clearly present these data points and offer actionable solutions.
It also helps to identify specific performance metrics to monitor — those that are most related to your goals. Concentrating on a few key metrics will help you stay focused on your priorities and continue making progress.
Mistake #5: Poor Communication
Communication is critical when you’re managing a fleet, regardless of its size. However, many fleet managers fail to implement and stick to a clear and effective communication strategy.
Poor communication leads to confusion and frustration for both managers and drivers. It can also lead to late arrival times and unhappy customers or clients.
What to Do Instead
There are several tools you can use to improve communication.
Consider using a Very High Frequency (VHF) fleet radio system equipped with Bluetooth and GPS location tracking. You can also use smartphone apps that help with route planning and make it easy for you and drivers to stay in touch.
Whichever communication option you choose for your team, make sure everyone uses them consistently and knows how they work. Otherwise, there’s no point in investing in them.
Mistake #6: Neglecting Training
As a fleet manager, it’s up to you to ensure your drivers are trained and ready to handle what the roads throw at them. They need the proper licenses, of course, but their training shouldn’t stop there.
Training is vital when you consider how quickly vehicles and technology are changing. Without ongoing training, you could be putting your drivers at risk.
What to Do Instead
Prioritize routine training for your drivers. Start with an in-depth training program for new drivers, but don’t let long-term employees off the hook, either.
Schedule regular refresher courses and continuing education courses to ensure everyone is up to speed. They need to stay informed about the company’s policies, road laws and regulations, and the specific features of their delivery vehicle.
Improve Your Heavy-Duty Truck Fleet Management Strategy Today
From ineffective strategies and poor communication to a lack of training, a lot can go wrong when it comes to heavy-duty truck fleet management. The good news, though, is that a lot can go right.
Follow the guidelines mentioned above to manage your fleet more effectively and set your business — and your drivers — up for success.
If you need help with maintenance or repairs for your trucks, we’re here to assist at All Things Truck and Trailer. Contact us today to learn more about our services or schedule an appointment.
Other Posts
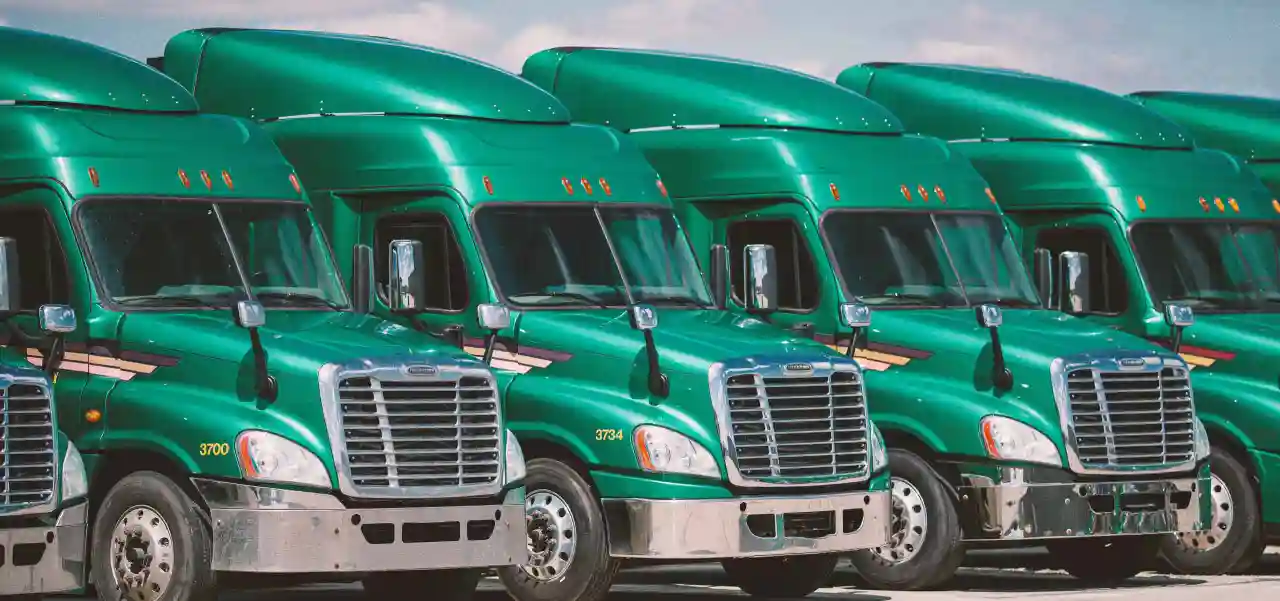
The Role Of Heavy-Duty Truck Wraps And Decals In Fleet Management
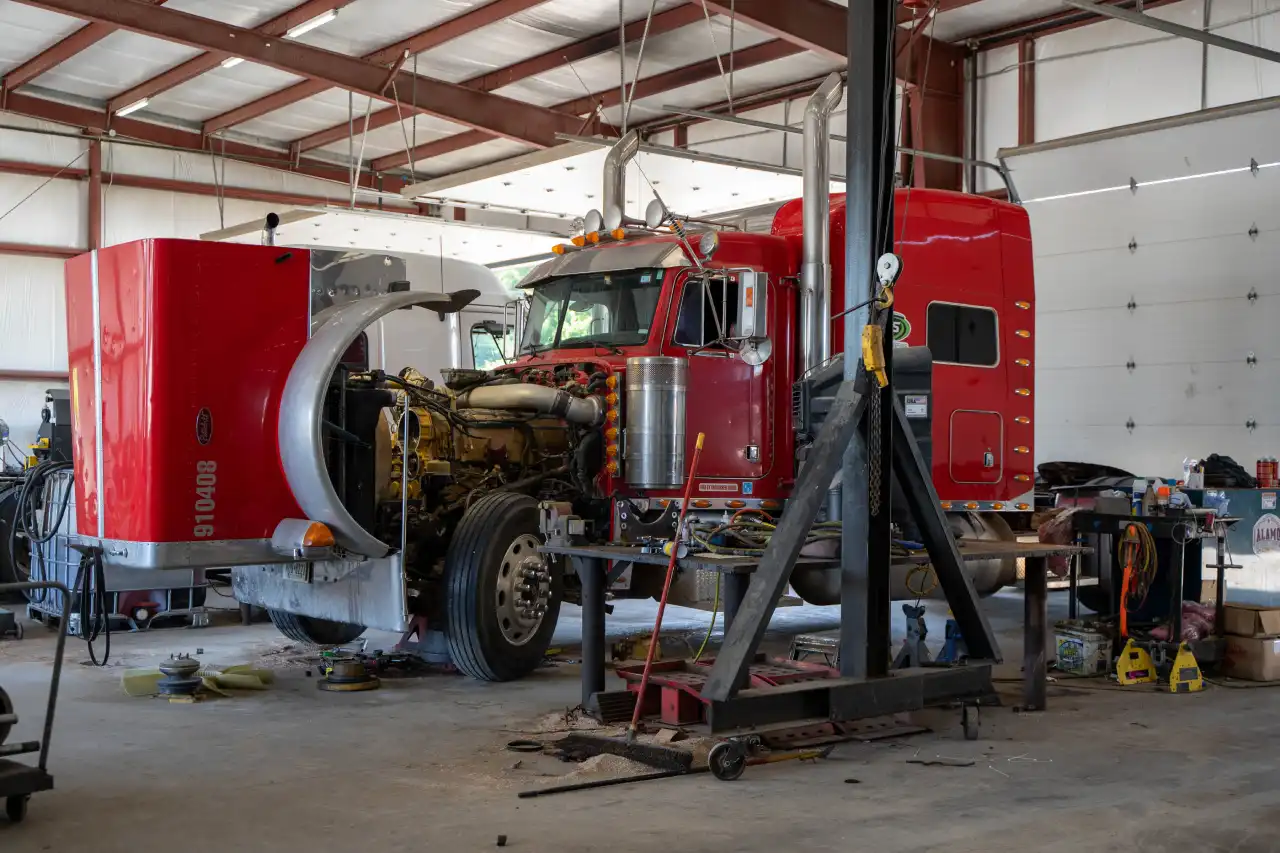
Choosing The Best Heavy-Duty Truck Repair Shop - 5 Things To Consider
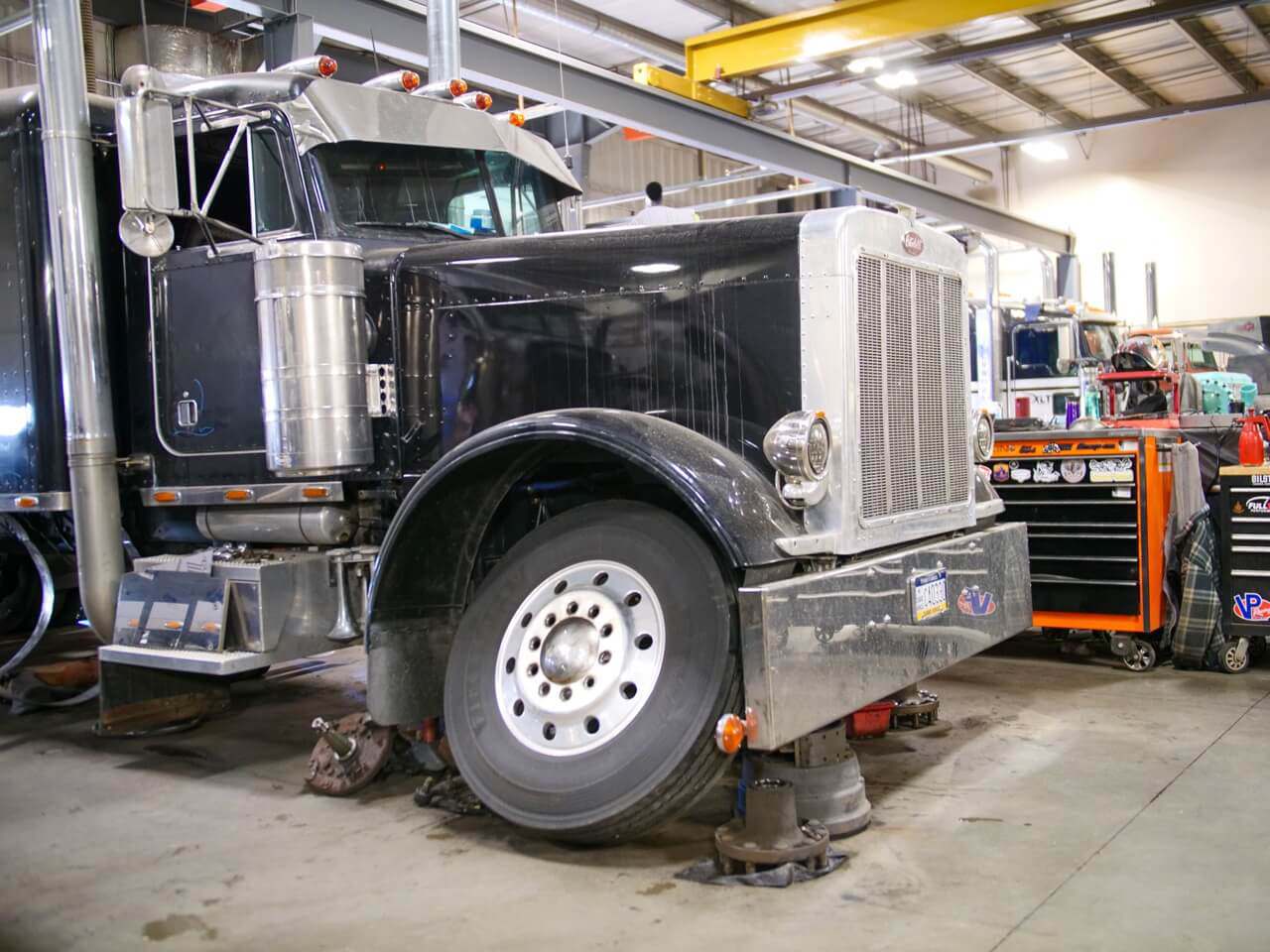